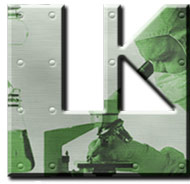 |
  |
|
 |
|
|
|
|
|
|
|
|
|
|
|
|
|
|
|
|
|
|
|
|
STATEMENT OF POLICY |
|
LeKem, a manufacturer of Electroless Nickel, recognizes
the need to ship products conforming with vendors’ and the customers’
specifications.
All of LeKem’s employees have been instructed that quality is
the highest priority we have (excluding safety). Our incoming inspections,
labeling, storage and procedures are written with this in mind.
Succeeding sections of this manual will amplify and describe how the
Quality Assurance (QA) program works. |
|
SCOPE |
|
The QA program is designed to insure that customers
receive the correct material, properly labeled in containers meeting
all Safety Standards.
The program includes: |
|
|
1) Incoming inspections of containers (bulk chemicals). |
|
|
2) Proper wording and use of labels. |
|
|
3) Communications to our customers of hazards with purchased chemicals. |
|
|
4) Retained samples and shipments. |
|
|
5) Training of supervisors and hourly personnel with proper procedures. |
|
RESPONSIBILITY
|
|
The president will establish Corporate Quality Assurance
Policy. |
|
|
|
|
|
QUALITY ADMINISTRATION |
|
A) General Manager - will have responsibility for and
will supervise the administration of the Quality Assurance Program. |
|
|
|
B) Sales – The General Sales Manager is responsible
for: |
|
|
1) Determining (where applicable) the end use of the
chemical being sold to customer. |
|
|
2) Determining grade of product (Tech, USP, Food Grade) wanted by
customer. |
|
|
3) Issuing (as needed) confirming specs to customers. |
|
|
4) Establishing that use by the customer is not in obvious violation
of any State or Federal regulations. |
|
|
5) Initiating customer complaint investigations. |
|
|
|
|
C) Operations – The operations Manager is responsible
for: |
|
|
1) Writing and issuing QA procedures to all warehouse and shipping
personnel. |
|
|
2) Insuring compliance with procedures. |
|
|
3) Training supervisory personnel in QA procedures. |
|
|
4) Writing label copy and up-dating labels. |
|
|
5) Reviewing and mailing pertinent safety and health information
to customers. |
|
|
6) Mailing MSDS (Material Safety Data Sheets.) to customers. |
|
|
7) Maintaining compliance with all State and Federal regulations. |
|
|
8) Working with Sales Manager on investigations of customer complaints. |
|
|
9) Disposition of rejected and / or off – quality chemicals |
|
|
|
|
D) Quality Assurance – Director of Quality Assurance
is responsible for: |
|
|
1) Inspection of incoming chemical deliveries (Metal and Acids) |
|
|
2) Inspection of returned goods for quality of products, specifications,
etc. |
|
RECEIVING INSPECTION |
|
A) Purchased chemicals (non – bulk) |
|
|
1) All factory sealed bags and drums are checked for
general container appearance and that product is what was ordered
(check against copy of PO issued by Purchasing to Vendor). |
|
|
2) Checked for proper labeling and hazard warnings. |
|
|
3) Damaged and / or incorrect product is refused at pick-up point
(by our driver) or at our dock if arriving via common carrier. |
|
|
4) Material received and subsequently determined to be off-spec
is tagged as such and held in a quarantine area pending disposal (usually
returned to Vendor). |
|
|
|
|
B) Purchased Chemicals (bulk): |
|
|
1) Samples are taken upon receipt at LeKem Warehouse and prior to
unloading. They are visually inspected for color, odor and clarity. |
|
|
2) Samples are sent to the laboratory for analysis. |
|
|
3) A sample is completely labeled with date, lot number, vendor,
and put in the Retained Sample Room for 12 months. (Disposed in an
environmentally sound method). |
|
|
4) Certificates of Analysis (where applicable from vendor) are filed. |
|
LABELING AND MSDS HANDLING |
|
1) Label copies for all chemical is determined by the
Operations Manager using all available information including: |
|
|
a) Vendor’s labels |
|
|
b) MSDS data |
|
|
c) ANSI Standards |
|
|
d) Government Regulations |
|
|
e) Good Manufacturing Practices |
|
|
|
|
2) Label copy is stored in a central computer. It can
only be changed by order of the Operations Manager. |
|
|
|
3) No finished label inventories are maintained. Labels
are printed daily as needed insuring that only the most recent labels
are used. |
|
|
|
4) A permanent, historical label file is maintained
by the operations. |
|
|
|
5) Manager to keep copies of all current and past labels. |
|
|
|
All repacked chemicals (1- gallon up to 55- gallon)
are labeled in one or two locations on each package. The computer
freshly prints applicable labels. Lot numbers are inserted on all
labels as are clock numbers of the persons filling the containers.
Both insertions are for tracking purposes if needed. |
|
|
|
|
|
MSDS |
|
1) A central file is kept of all MSDS received from
vendors. Vendor MSDS are reproduced verbatim and stored in a central
computer for: Easy access by all LeKem chemical personnel (including
Sales). |
|
Computerized mailing to: |
|
|
1) New customers |
|
|
2) Old customers purchasing new products. |
|
|
3) MSDS are mailed to all customers when they purchase. A product.
Permanent hard-copy files are kept of what MSDS were mailed to each
customer. |
|
|
4) MDS sheets are updated as new information is received from vendors. |
|
|
|
|
|
|
 |
|